Design of a Garlic Chopper

Problem
MSC International decided to create a garlic gadget that would finely chop garlic in a fast and efficient manner. The main problem with dicing multiple garlic cloves with a knife is that not only it takes some time but your fingers gets also smelly in the process. The main goal was to make a device that could dice 1 to 4 garlic cloves at once in a minimal amount of time.

Existing products
When this project was started in 2008, multiple devices were already on the market, the most popular being the patented Garlic Twist and the Garlic Zoom from Chef’n. The Garlic Twist is a very simple design, which is easy to clean. The Garlic Zoom is very original, playful and compact which I liked. However, after testing extensively both items with numerous others, we found that they were limited in their capacity and it was a bit of a hassle when doing multiple cloves.

Preliminary Concepts and Sketch
We explored several possibilities to achieve our set goals : Dicing press, mandolines, rotating blades and other contraptions. The general direction that seemed more realistic and reliable was the rotating blade concepts. At this point I just sketch anything that comes up to mind.
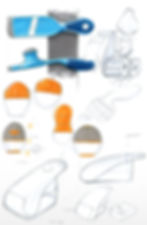
Early Mechanical Idea
We decided pretty early on to use manually powered rotating blades. We wanted the blade’s rotation to turn faster than the user would turn the then undefined handle/grip part. This meant we needed to use gears but it was also important to have decent torque so that the gears didn't skip when going through multiple cloves at the same time. Therefore, we choose an architecture that would revolve around an epicyclic gear which multiplies rotation and provides torque to the central spinning blade.

Final Digital Sketch
We had this idea of a compact round shape as seen in the sketch section of this post. Final sketch of the chopper made in Sketchbook Pro

Preliminary 3d
We settled on the shape below which would be refined as we added the mechanical components inside.

1st 3d printed prototype
Mock it up or fuck it up is words I live by in my practice. We tought that the speed of the blade would be sufficient for the blade to slice through but we were very wrong. The garlic can get stuck on the blade and rotates with it. A prototype that fails is a good prototype because I'd rather know now that my design doesn't work now rather than when it's on the shelves. Back to the drawing board. Prototype below is made using FDM (fused deposition modeling) on a Dimension 1200 machine.

2nd prototype
The principle we used was to put a central separator part that would stop the garlic while the blade cuts through it.

The first problem was that the central separator had ribs that were too long and caused the blades not to be able to go through the garlic. We subsequently chopped these down to a more reasonnable lenght.The results were promising but we found that the central part proved to be extremely difficult to clean.

This is the main problem with kitchen gadgets: you might make a task faster but your contraption is more difficult to clean thus canceling the saved time. We had to find something better. Also using 4 blades made the insertion of more garlic cloves difficult. So we opted for 2 blades for the next prototype.
3rd prototype
At this point we removed 2 blades and had to find an easy to clean solution to stop the garlic and would allow the blade to slice through it. The solution was ridges/ribs that were intergrated into the clear body of the item. We had to make a couple prototype to find the right height and geometry of this detail. Pictured below is the first pre-prodution sample from the tooling using this solution.

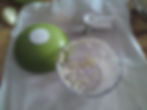
It works !
Final product
At this stage there is a lot of back and forth with the supplier to fix produciton issues such as flashing, improper molding,etc. In the end we got a sample that satisfied the quality that we wanted and went into production.
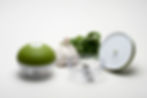
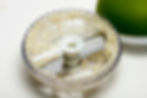
Technical details and Material used
Green soft grip – Thermoplastic rubber (TPR) overmolded on a Polypropylene (PP) base (TPR and PP bonds well together)
White – PP was used because we needed details soft enough to snap the gears in place. Also PP is very cheap.
Gears – Acetal. Very stable plastic, low shrink rate, very appropriate for plastic gears
Clear bottom – Styrene-Acrylonitrile (SAN). Clear and cheap transparent material often used in kitchenware. Other transparent resins could have been Acrylic (PMMA) or Polycarbonate (PC) but they both have flaws for this design : PMMA is brittle and not dishwasher safe while PC contains BPA which we tend to avoid when parts are in contact with food.
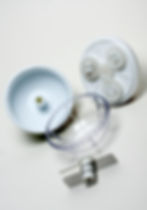

See the product in action in the link below